In the fast-paced retail and food service industries, effective inventory management is crucial for maintaining optimal stock levels, reducing waste, and enhancing customer satisfaction. Traditional inventory management methods are labor-intensive and prone to errors, leading to significant operational inefficiencies. Recognizing the need for a more efficient, accurate, and real-time inventory monitoring solution, our client embarked on an initiative to automate and improve the inventory visibility of items stored within refrigeration cabinets.
In an effort to stay ahead in the competitive landscape of the retail and food service industries, our client recognized the imperative need for innovation in inventory management practices. With a vision to transcend traditional, labor-intensive methods prone to inaccuracies, they approached us to spearhead a project on “Software Agnostic Camera Technology“.
Client Overview
Client is major company that operates in the Food & Beverages industry. The client also having a multinational chain of ice cream and beverage specialty shops that stores the eatables in the ice cream cabinets.
Engagement Objective
The primary objective of this engagement was to identify partners capable of providing innovative software agnostic camera modules. These modules needed to be capable of capturing regular still images of the stock items within refrigeration cabinets and seamlessly sharing this data on a cloud platform. The initiative aimed to address several key points:
- Identification of Products/Solutions: Discovering products and solutions related to software agnostic camera modules offered by potential partners, focusing on features, specifications, and pricing information.
- Identification of Top Partners: Determining the best partners based on various criteria, including pricing, capabilities, timelines, product and solution features, and specifications.
Engagement Outcome Snapshot
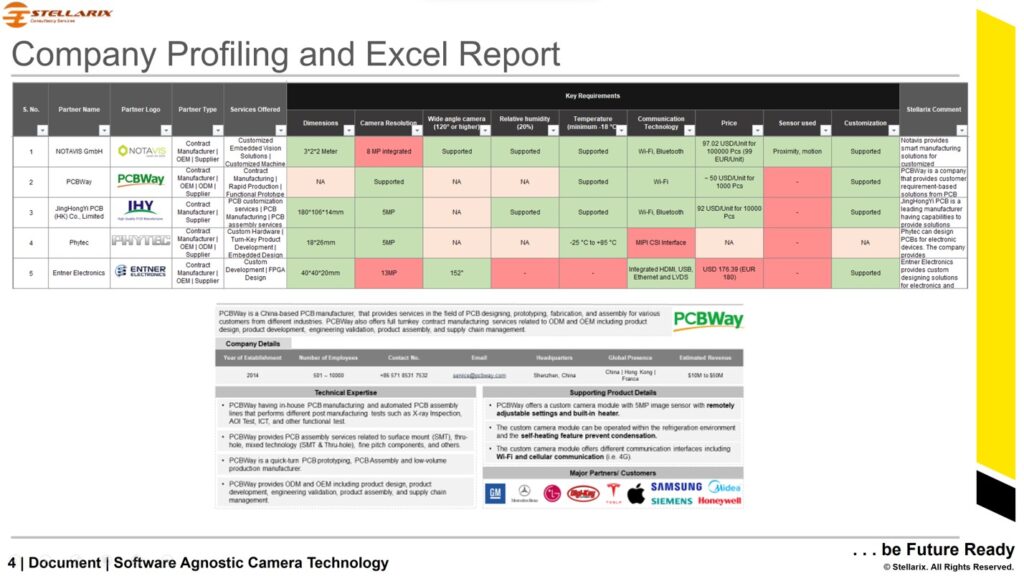
Business Benefits
This comprehensive study helped our client by providing them with the necessary tools and insights to select the optimal partner for procuring or manufacturing the ideal software-agnostic camera module. These specially designed modules are engineered to be installed within refrigeration cabinets, adept at capturing high-quality still images of the stock items. These images are then efficiently uploaded to a designated cloud platform, facilitating further analysis and inventory management optimization.
- A meticulously curated list of 161 potential partners was presented to the client with critical details for each partner, categorized into three distinct groups: solution providers & integrators, electronic manufacturing service providers, and custom camera manufacturers. We also provided an in-depth profiling of the top 5 partners from each category. This selective shortlisting was based on a rigorous benchmarking process, evaluating each contender against a set of critical parameters.
- The benchmarking score played an important role in the partner selection process, ensuring that the chosen partners not only met but exceeded our client’s expectations in terms of technical requirements and operational feasibility.
By engaging in this detailed study, our client was positioned to make a well-informed choice among a vetted list of partners, each capable of delivering a cutting-edge solution tailored to their specific needs. This strategic selection process paves the way for enhanced inventory visibility and management, leveraging the latest in camera module technology to drive efficiency, reduce waste, and ultimately foster a competitive edge in the retail and food service sectors.