Lithium-ion batteries are commonly used in electric vehicles due to their high energy density and long cycle life. The temperature has a huge impact on lithium-ion battery performance and longevity, therefore it's critical to keep them in the appropriate range. EV batteries reach their end-of-life once they reach a 20 percent capacity loss or 30 percent internal resistance growth. Both active and passive Battery Thermal Management Systems (BTMS) are the main cards that engineers play to tackle battery overheating and poor performance. There are various types of BTMS techniques based on the purpose, source and cooling medium. Efficient temperature management systems contribute significantly to battery health and extend the overall lifespan. Moreover, as the capacity, charge and discharge rate increases, battery’s security issues need more attention. Subsequently, various BTMS have been developed to meet the demand for higher power, faster charge rates, and improved driving performance. In passive BTMS, phase-change materials, heat pipes, aerogels, hydrogels, etc. are utilized, with the benefit of no additional power consumption. On the downside, the cooling process is difficult to manage.
Thermal Model and Issue
Li-ion batteries generate heat during charging and discharging in three forms, i.e., electrochemical reaction polarisation, joule heating producing ohmic losses, and reversible reaction heat due to entropy change. Insufficiently releasing the heat generated by the battery during charging or discharging can compromise battery performance, life, and safety. Temperature greatly influences the behavior of any energy storage chemistry. Also, lithium-ion batteries (LIBs), in particular, play an important role in the energy storage application field, including electric vehicles (EVs). The battery thermal management system is essential to achieve the target.
EV Battery Management System Market
In 2021, the global market for electric vehicle battery management systems was valued at $1.42 billion. Experts predict that this market will experience significant growth, with an expected compound annual growth rate (CAGR) of 17.2% from 2022 to 2027. By 2027, the market is anticipated to expand to a value of $5.67 billion.
Integrating LIBs into an application requires understanding how temperature affects the essential cell components and their governing equations. The speed of chemical reactions and/or the mobility of the active species may alter dramatically if the battery is exposed to harsh thermal conditions or if the optimum temperature cannot be maintained. The change in LIB characteristics as a function of temperature may cause, at best, a performance issue and, at worst, a safety issue. Even though there are several studies on BTMS for LIBs in the literature, their industrial implementation remains a challenge.
Thermal Runaway
Today, the major problem caused by the heat of the Li-ion batteries is a thermal runaway. When thermal runaway occurs, it accelerates the temperature increase, resulting in destructive consequences such as rapid temperature rise, gas generation, and even battery explosions. This phenomenon has a very negative effect on the safety of vehicles and passengers. Moreover, thermal runaway can be prevented with safety vents, automated reset devices, coatings, thermal fuses, shutdown separators, chemical shuttles, and heat-retardant electrodes and electrolytes.
In addition to these safeguards, it is important to prevent the non-uniform temperature of battery cells, which is the main cause of thermal runaway.
Classification of Battery Cooling Systems
The battery thermal management system with a vapor compression cycle includes cabin air cooling, second-loop liquid cooling, and direct refrigerant two-phase cooling. The battery thermal management system without a vapor compression cycle includes phase change material cooling, heat pipe cooling, and thermoelectric element cooling.
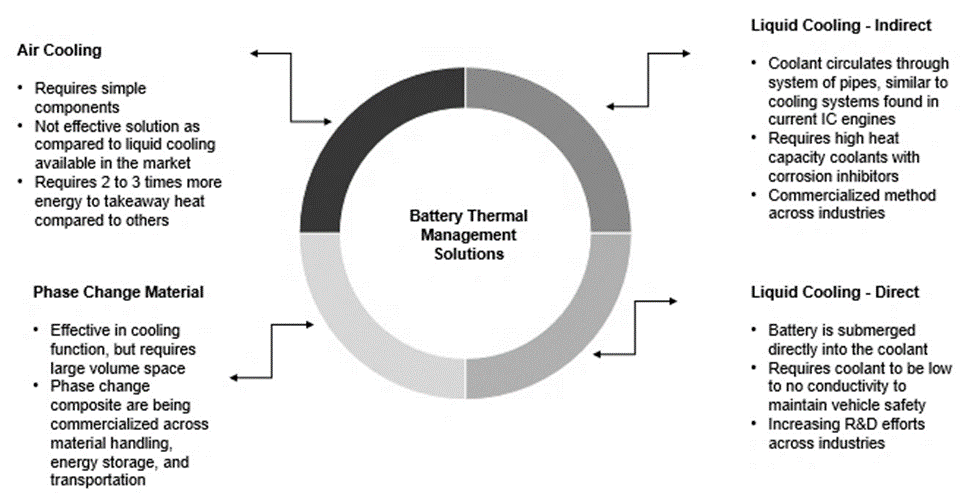
The BTMS has a crucial function. It maintains an optimal operating temperature range and ensures a uniform temperature distribution within the battery cell module. This is done at high charge/discharge rates, and it also works in extreme external environmental conditions.
Immersion Cooling
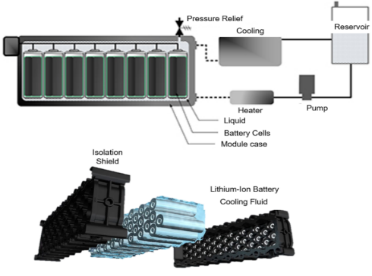
Immersion cooling entails submerging the battery cells in a liquid coolant. Furthermore, the fluids’ flame-retardant properties are a safety feature, preventing thermal runaway events before they spread between cells.
As manufacturers look for an alternative to traditional battery cooling systems, direct immersion cooling systems could provide the best option in the future.
Depending on the properties of the coolant, the immersion cooling techniques are classified as:
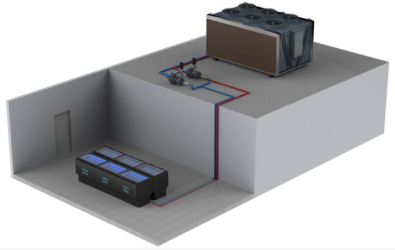
Single-phase Immersion Cooling:
Single-phase coolant never changes state, it never boils or freezes and always remains in a liquid form. The coolant gets pumped to a heat exchanger where heat is transferred to a cooler water circuit. In addition, this technique uses “open baths“, as there’s a little (or no) risk of the coolant evaporating. Also, the battery cells are entirely immersed in a dielectric heat-transfer fluid (dielectric coolant). Direct conduction is commonly used to circulate the dielectric coolant, which absorbs heat from the cells.
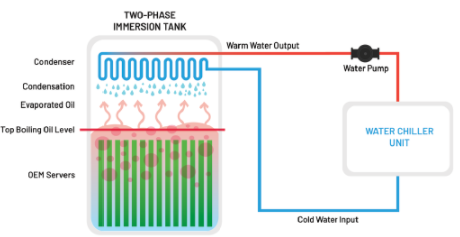
Two-phase Immersion Cooling:
The working fluid boils and thus exists in both a liquid and gas phase. The system takes advantage of a concept known as “latent heat,” which is the heat (thermal energy) required to change the phase of a fluid. Moreover, the working fluid is only cooled by boiling and thus remains at the boiling point (“saturation temperature”). Energy is transferred from the heat source into the working fluid, and this causes a portion of it to boil off into gas. Furthermore, the gas rises above the fluid pool, where it contacts a condenser which is cooler than the saturation temperature. This causes the fluid to condense into a liquid and fall (rain) into the pool.
Key Players
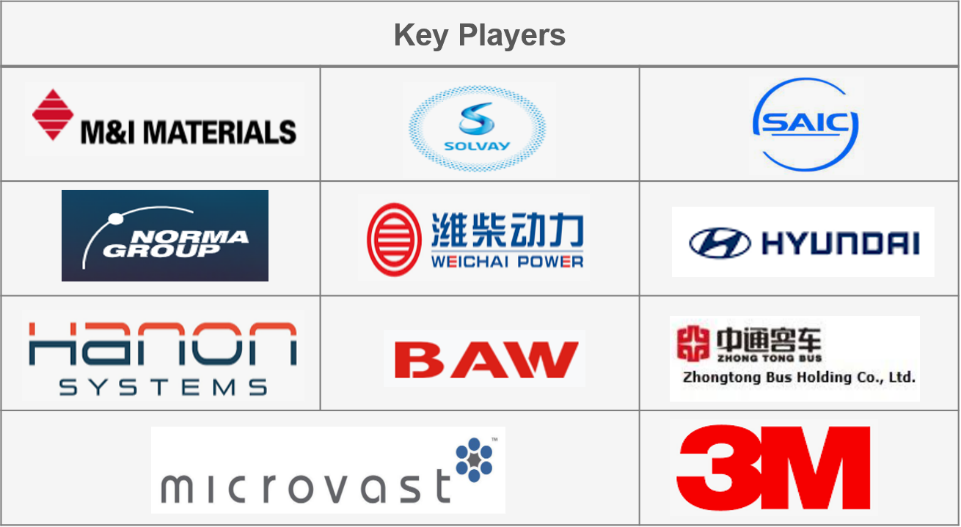
Many companies, including Hyundai, 3M, Solvay, and Microvast, are actively conducting research in this area. A few of the inventions are given below:
- Hyundai WIA developed the first thermal management system for electric vehicles with an integrated coolant distribution supply module.
- 3M provides bonding, cooling, cushioning, grounding, and sealing of batteries. Efficient and effective thermal management solutions are provided throughout the entire process. Streamlined processes are ensured. Assembly is faster. Battery systems for xEVs are designed. They have extended life. They offer an increased range. Recharge time is reduced.
- Solvay provides specialty polymers for battery and fuel cell solutions. It is dedicated to providing material solutions for batteries that allow customers to produce energy storage systems that are safe, reliable, and long-lasting.
- Microvast non-flammable battery technology has gained considerable attention in recent years. The non-flammable electrolyte ensures both ultra-fast charging and long battery life. Further, it reduces the possibility of thermal runaway and short-circuiting.
Active Universities
- Guangdong University of Technology: At Guangdong University, research has been conducted on a composite phase-change body that is filled with the phase-change material to obtain better uniformity of battery-pack temperature.
- Wuhan University of Technology: Wuhan University is focusing its research on a circulating device of an electric vehicle battery thermal management system and a controlled method of the circulating device.
- Jilin University: Researchers at Jilin University have developed a hybrid system of liquid-cooled Battery Thermal Management System (BTMS) and Heat Pump Air Conditioning system (HPACS) for battery electric vehicles (BEV). An automatic calibration model of the liquid-cooled BTMS-based HPACS is established to predict the cooling capacity and system Coefficient of Performance (COP) of the BTMS by Support Vector Regression (SVR).
Importance of Thermal Management in Attaining EV’s Full Potential
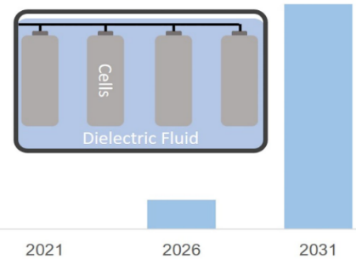
Ultrafast charging is a prominent topic in the electric vehicle business. Additionally, If a car can be charged in less than 30 minutes, its range anxiety is reduced. In addition, this capacity has now been added to a number of automobiles on the market. With the Porsche Taycan/Audi e-tron GT platform and the new Hyundai E-GMP design, more examples of 800 V systems are coming. These higher voltages also make charging go faster. On the other hand, thermal management is an important concern for fast charging. Keeping the batteries cool during this process not only helps extend the cells’ life but is also a critical safety element to prevent thermal runaway.
Important Aspects of EV Battery Thermal Management
- Temperature Range: The optimal temperature range for Li-ion battery packs is 20°C to 45°C. Cold battery pack temperatures can reduce charge/discharge capacity and power capabilities, while high temperatures can result in performance degradation, loss of capacity, and increased internal resistance.
- Heating and Cooling: BTMSs have two primary functions: heating and cooling. The battery pack may need to be heated in cold ambient conditions to facilitate charging, pre-conditioning, and achieving the ideal pack temperature. Conversely, it may need to be cooled in hot ambient conditions to maintain its optimal temperature range.
- Liquid Cooling: Liquid cooling is considered an effective approach to maintain the battery temperature in a suitable range, allowing significant efficiency improvements. Coolant is utilized in liquid-cooled battery packs to facilitate the transfer of heat between the battery cells and the Battery Management System (BMS). This heat exchange can occur through direct immersion or conduction via a battery plate or another supporting structure.
- Challenges in Cold Climates: In cold climates, batteries may need to be heated when temperatures fall, and under fast charging or extra fast charging (XFC) conditions, batteries may require additional levels of cooling
Future Perspective
As a result, we’ve seen a surge in interest in various cutting-edge technologies like immersion cooling. Further, electric vehicles will scale up only when various designs and approaches regarding BTMSs are considered. Also, applying and integrating the proposed novelty systems and models could improve full-size battery packs’ thermal and energy efficiency.