Liquid Cooling for Data Centers
Globally, the data centers industry is experiencing an increasing data requirement primarily driven by the number of internet users and a significant need for faster internet speed. For example, from 2017 to 2022, the number of global internet users increased by more than 50%. Further, during 2017-2023, the average global internet speed has grown by more than six times. So, the role of liquid cooling in modern data centers has become crucial.
As a result, the data centers consistently push the technological boundaries to pack in as much computation power as possible per unit area. For example, from 2017 to 2022, the average global server rack density almost doubled from 5 kW to around 8-10 kW. Hence, there is a growing demand for advanced technologies, including advanced cooling solutions to accommodate the high rack densities. Liquid cooling offers the ideal solution for the data centers of the new age as it achieves significantly superior capabilities over conventional air cooling solutions.
What is Liquid Cooling, and Why Now?
The liquid cooling method utilizes thermally conductive, dielectric liquid coolants to absorb the heat from the IT equipment and cool them down. Liquid coolants are 1000 times more efficient than air; liquid cooling can support high equipment density and devices that generate higher than average heat. Liquid cooling finds applications in high-density and edge-computing data centers, amongst others.
Traditional data centers have low density and have prominently opted for air-cooling solutions. However, the IT industry has witnessed a revolution in the last decade owing to the adoption of artificial intelligence (AI), data analytics, and Internet of Things (IoT) technology.
AI: The rapid adoption of AI has had the most prominent impact on data center density. AI is designed to handle an unprecedented amount of data; hence, the demand for packing more computing power in each piece of equipment has risen.
Data analysis: It requires high-performance computing as it processes data from a myriad of sources.
IoT: As of 2023, 15.14 billion smart devices are connected through the internet, a more than 75% increase compared to 2019. Further, the IoT industry is expected to retain this exponential growth over the next few years, as the number of IoT-connected devices globally is expected to double between 2023 and 2030. As IoT is designed to process data from connected devices in real time, the growth of the IoT sector also contributes to the demand for higher computational power and computation power density.
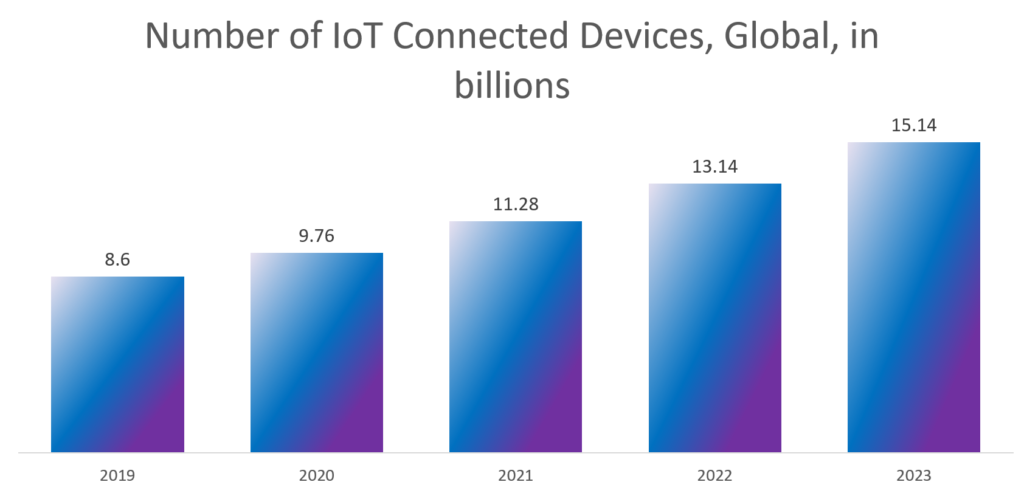
Figure 3: Number of IoT Connected Devices Globally
As a result, although until very recently it seemed that a rise in the rack densities to the level unsupportable with air cooling is too optimistic, in the last 2-3 years, data centers have been built with high-performance computing (HPC) with rack density of up to 200 kW. Hence, unlike traditional data centers that use liquid cooling with air cooling, some modern data centers rely entirely on liquid cooling. Further, with the expected high-paced adoption of AI, data analytics, and IoT, the data center rack densities will continue to grow in the coming years, with HPC accounting for a significant share of the global data center capacity. This trend will ensure a strong growth in the adoption of liquid cooling technology.
Types of Liquid Cooling Systems in Data Centers
Liquid cooling can be achieved through different mechanisms with unique advantages associated with each technology. Based on the design approach, there are two main types of liquid cooling methods: immersive liquid cooling and direct-to-chip liquid cooling. Immersive liquid cooling is further segmented into single-phase and two-phase immersive liquid cooling.
- Immersive liquid cooling: In this method, the electric device is placed inside dielectric liquid. The liquid absorbs the heat generated by the device.
- Single-phase immersive liquid cooling: The IT equipment is immersed in this system’s thermally conductive, dielectric liquid coolant. The coolant absorbs the heat from the IT equipment and heats up. The warm coolant is fed to a heat exchanger, which exchanges heat with the cold water. The resulting cool liquid coolant is recirculated to the immersive liquid cooling system. In single-phase immersive liquid cooling, the coolant does not evaporate and always stays in the liquid form. The single-phase immersive liquid cooling offers several advantages, including low fluid loss, non-toxicity, low cost, and lower maintenance.
- Two-phase immersive liquid cooling: Similar to a single-phase system, IT equipment is immersed in the dielectric coolant to absorb the heat in a two-phase system. However, instead of cooling the heated liquid in a heat exchanger, the coolant undergoes a low-temperature evaporation process. The resulting gas is cooled again using a condenser coil to return to the liquid form. This method does not use a heat exchanger, so it achieves better Power Usage Effectiveness (PUE) than the single-phase system.
- Direct-to-chip (DTC) liquid cooling: The DTC method, also known as cold plate cooling, involves the circulation of the non-flammable dielectric fluid directly over the IT component through a highly conductive cold plate to dissipate the heat. The dielectric fluid absorbs the heat and turns it into vapor. This vapor is brought out of the equipment through the same tube.
Three main advantages offered by the DTC method over the immersive liquid method include high precision, high thermal resistance that enables efficient cooling, and low servicing & maintenance costs. On the other hand, immersive liquid cooling is simpler in design and offers better space efficiency, total cost of ownership, improved PUE, and higher flexibility.
Commercialized Innovations in the Liquid Cooling Space
Although both liquid and immersion cooling have disadvantages, some organizations have developed breakthrough technologies to address and achieve superior performance.
- Chilldyne: Chilldyne has developed a patented, innovative DTC liquid cooling design comprising negative pressure technology, which creates a vacuum to pull the water coolant through the cooling ecosystem. This design ensures that coolant never leaks, even in case of tube damage. Further, the design eliminates the need for costly and reinforced hardware, making it cost-effective and easy to install.
- CoolIIT Systems: CoolIIT Systems has developed copper-based cold plates with patented split-flow technology. The split-flow design comprises microchannel architecture, which helps minimize pressure drop, maximize coolant flow, and precisely direct the coolest fluid to the hottest area, maximizing efficiency. The unique approach enables compact plate design, enhancing the flexibility of the technology.
- CoolIIT Systems: CoolIIT Systems has developed copper-based cold plates with patented split-flow technology. The split-flow design comprises microchannel architecture, which helps minimize pressure drop, maximize coolant flow, and precisely direct the coolest fluid to the hottest area, maximizing efficiency. The unique approach enables compact plate design, enhancing the flexibility of the technology.
- Dug Technology: The company has developed an immersive liquid cooling system, DUG Cool, that uses proprietary polyalphaolefin dielectric fluid that is non-toxic, biodegradable, non-polar, and low viscosity. Further, the DUG Cool system reduces power consumption by 51% compared to conventional air cooling systems.
- Iceotope Technology Limited: Iceotope Technology has developed a DTC precision cooling system that precisely directs the coolant at the hottest areas to ensure maximum efficiency. As a result, Iceotope Technology’s cooling solution achieves 96% less water usage, 40% less power usage, and 84% less cooling usage.
- LiquidCool Solutions: The company has developed patented Total Immersion with Directed-Flow (TIDF) liquid cooling technology that combines DTC with immersion cooling. TIDF achieves higher computation density, a lower space footprint for the cooling system, a 1/3rd of the coolant tank requirement, and lower maintenance. The transfer fluid exits the heatsinks and immerses the other electronics to gather the remaining heat before leaving the chassis to be cooled and returned. The coolant is non-toxic and never needs to be replaced.
Conclusion
The inevitable growth in AI, data analytics, and IoT adoption is expected to force the data center industry to adopt HPC with rack densities unsupportable by air cooling methods. Hence, liquid cooling has become a necessity rather than a choice, driving exponential growth in its adoption. Such high adoption rates are also driving economies of scale and R&D in the industry, which, in turn, is making liquid cooling solutions economical and more comprehensive. Further, the unique approaches taken by the innovators in the industry are likely to push the performance boundaries for liquid cooling, which, in turn, will help the data centers achieve unprecedented computational power density in the years to come.