Advanced EV Battery Recycling
The industry’s rapid growth and increasing expansion emphasize the great significance of developing a sustainable and environmentally friendly economy. As a result, the growth of EVs has increased rapidly, which has led to the demand for EV batteries. Thus, the demand for raw materials increases, which raises the concern of EV battery disposal. Improper disposal of EV batteries will lead to an environmental impact. This emphasizes the urgent need for effective recycling technologies.
The Growing Importance of EV Battery Recycling
The widespread adoption of electric vehicles (EVs), powered by lithium-ion batteries, has been a significant step towards sustainable transportation, offering a cleaner alternative to traditional combustion engines. However, as these vehicles age and their batteries degrade, the need for efficient battery recycling becomes increasingly critical.
Lithium-ion batteries contain valuable materials such as lithium, nickel, cobalt, manganese, graphite, copper, and lead. Improper disposal or extraction of these materials can lead to severe environmental and health risks. Recycling these batteries mitigates these dangers and provides a vital source of rare metals essential for manufacturing new battery cells. These metals are often not readily available locally, so recycling is crucial in reducing dependence on imports. In fact, up to 95% of the metals in batteries can be recycled and repurposed for new battery production, contributing to more sustainable supply chains.
Battery recycling also offers significant environmental benefits. It can reduce the carbon emissions associated with battery production by as much as 90%, while simultaneously decreasing the need for raw material extraction. This helps prevent pollution and conserve natural resources, supporting a circular economy in the EV industry.
Additionally, the risks associated with informal recycling practices, such as the release of toxic gases during pre-treatment and processing, underscore the importance of adopting safe, formal recycling technologies. Effective recycling not only strengthens local supply chains but also minimizes the environmental impact of battery production and disposal.
EV Battery Recycling Technologies
- Mechanical Recycling: This method involves physically breaking down the battery into smaller pieces. The process typically includes:
- Shredding: The batteries are disassembled and shredded into smaller parts.
- Sorting: The materials are sorted based on physical properties like size, density, and magnetism.
- Separation: Different materials, such as metals (e.g., copper, aluminium) and battery components, are separated for further processing.
- Hydrometallurgical Recycling: This process uses aqueous chemistry to extract valuable metals from the battery materials. The steps typically include:
- Leaching: The shredded battery material is treated with chemicals to dissolve metals like cobalt, nickel, and lithium.
- Separation: The metals are then separated using methods such as solvent extraction or precipitation.
- Purification: The extracted metals are purified and recovered as salts, which can be used to produce new battery materials.
Hydrometallurgy offers several benefits, such as it can recover up to 98% of valuable metals, and the process often operates at lower temperatures than pyrometallurgy. It produces less waste and fewer emissions. However, it also has drawbacks, such as hazardous chemicals that can pose risks, and the process can be technically challenging.
- Pyrometallurgical Recycling: Pyrometallurgical processes involve using high temperatures to melt and separate metals in the battery. The steps typically include:
- Incineration: The batteries are heated to high temperatures to burn off non-metallic components, leaving behind a mixture of metals
- Smelting: The remaining materials are melted and separated based on their melting points, allowing the recovery of valuable metals like cobalt, nickel, and copper
Key Developments in EV Battery Recycling Technology
Recent developments in battery recycling technology are driving significant advancements in electric vehicles (EVs), making them more efficient, powerful, and cost-effective.
Key innovations include:
- Mechanical-Hydrometallurgical Recycling: Mercedes-Benz has opened Europe’s first battery recycling plant with an integrated mechanical-hydrometallurgical process. The plant covers all steps from shredding battery modules to drying and processing active materials. The mechanical process sorts and separates plastics, copper, aluminium, and iron, while the hydrometallurgical process focuses on extracting valuable metals, like cobalt, nickel, and lithium, from the black mass in a multi-stage chemical process. These recyclates are refined for use in new batteries.
- Hydro-to-Anode® Graphite Recycling Technology: Ascend Elements and Koura have partnered to commercialize the Hydro-to-Anode® graphite recycling technology. This technology produces 99.9% pure graphite from end-of-life lithium-ion batteries and manufacturing scrap, providing a new source of battery-grade anode materials for North America’s electric vehicle market.
For a deeper exploration of graphite’s role in sustainable battery production and circularity, read our full article on Graphite Repurposing: A Circular Economic Perspective
Partnerships and Collaborations
- Stena Recycling and BASF are collaborating to improve black mass production processes for higher recovery rates, supporting closed-loop solutions. Stena will collect, assess, and pre-treat end-of-life lithium-ion batteries and production scrap to produce black mass. This black mass, containing valuable metals, will then be refined at BASF’s prototype metal refinery.
- Altilium and Enva have signed an MOU to collaborate on EV battery recycling, focusing on the safe handling and collection of batteries across the UK for recycling using Altilium’s EcoCathode™ process. This advanced hydrometallurgical process recovers over 95% of battery metals, which can be reused in new battery production.
Key Players in the EV Battery Recycling Industry
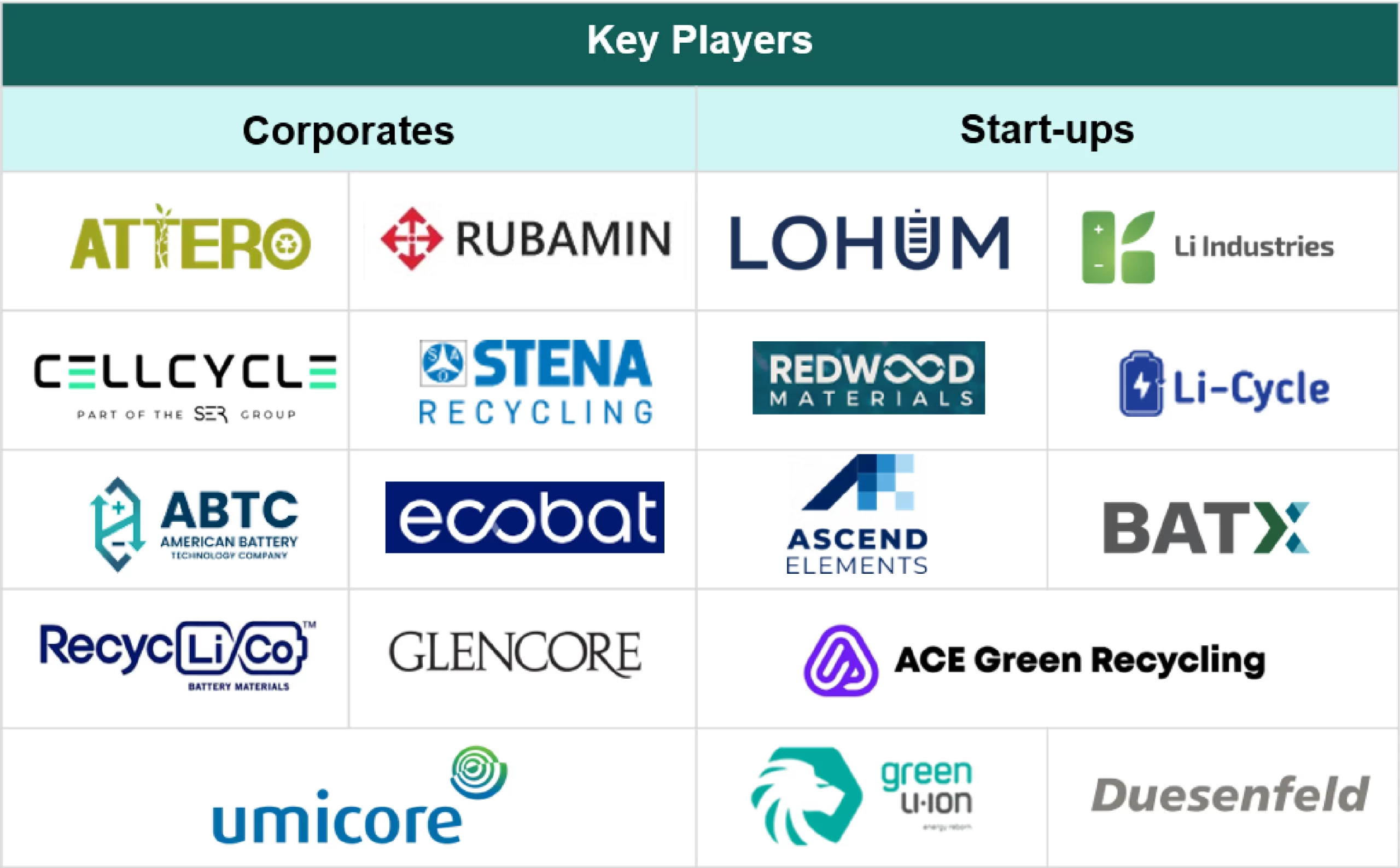
The key players in the industry are listed below, followed by an explanation of Duesenfeld’s recycling technology. Innovative Duesenfeld process chain for Recycling Lithium-Ion Batteries:
1. Discharging: The recycling of lithium-ion batteries starts with a deep discharge method that effectively and safely removes the batteries’ energy. Regardless of the battery’s age, manufacturer, voltage, or charge state, the Duesenfeld procedure uses intelligent software to automate this discharge. The quick and effective process is guaranteed by this high-power discharge.
2. Mechanical Processing: After discharging and dismantling, the batteries are shredded in an inert gas environment. After that, vacuum distillation is used to recover the electrolyte solvent. There is no need for exhaust gas treatment since a low process temperature restricts the production of harmful gases. The electrode scraps are shredded and immediately moved to the next stage, without requiring drying. After being sorted according to shredded material size, density, and magnetic properties, the shreds are subjected to additional processing. Iron, copper, and aluminium are sent to conventional recycling streams. The remaining substance, called Black Mass, is treated using a unique hydrometallurgical process to recover important metals such as cobalt, lithium, nickel, manganese, and graphite.
3. Hydrometallurgy Process: Only cobalt and nickel are recovered in the majority of industrial hydrometallurgical procedures for recycling black mass; lithium, manganese, and graphite are lost and eliminated from the material cycle. Before the leaching procedure, a pre-treatment step that eliminates the fluoride prevents hydrogen fluoride from forming. After that, the metals are leached and separated from the graphite. Cobalt, nickel, lithium, and manganese are then separated, purified, and recovered as salts. These salts are used as raw materials to produce new cathode active materials.
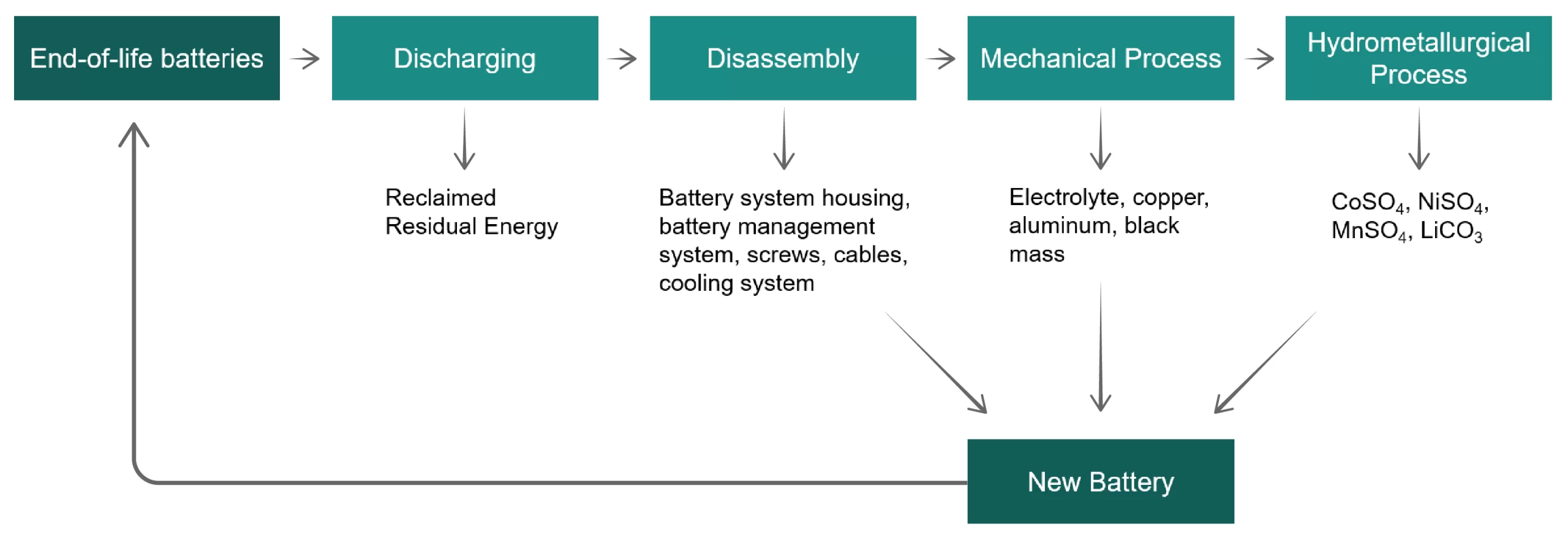
Conclusion
In conclusion, the demand for critical materials like lithium, cobalt, and nickel grows, making recycling an essential strategy to reduce reliance on mining & mitigate environmental impact. The recycling methods outlined—hydrometallurgy, pyrometallurgy, mechanical procedures, and emerging trends—offer promising sustainable solutions for managing EV batteries.
Efforts to establish closed-loop systems enable used batteries to be repurposed or reintroduced into the manufacturing cycle to a circular economy. Ongoing research and development in this area are essential to ensure resource sustainability, reduce environmental harm, and pave the way for a greener, more energy-efficient future. Consumers, manufacturers, and policymakers must focus on the responsible disposal and recycling of EV batteries. By working together, the EV industry can promote a circular economy that optimizes resource recovery while reducing waste.